65 هزار بشکه نفت در روز؛ دستاورد یکپارچگی داده و هوش مصنوعی
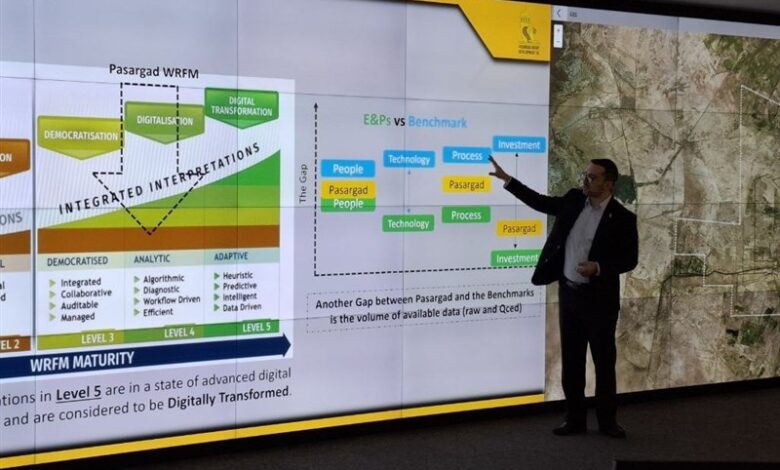
به گزارش خبرنگار اجتماعی آرمان خبر، برنامه بازدید از مرکز مدیریت یکپارچه چاه، مخزن و تأسیسات حوزه نفت (WRFM) بهعنوان نخستین پروژه واقعی در حوزه هوش تجاری با هدف حرکت به سمت هوش مصنوعی در صنعت نفت، با حضور خبرنگاران برگزار شد.
دکتر سید مهدی سیدسار؛ رئیس پورتفولیو معاونت بالادستی شرکت دانشبنیان انرژی پاسارگاد در این نشست اظهار کرد: ما در این جلسه قصد داریم ماژول سیستم هوشمند و مدیریت همزمان چاه و مخزن را که در گذشته شروع به توسعه آن کردهایم، معرفی کنیم. شاید اهداف زیادی را بتوان برای این مرکز برشمرد، اما اگر بخواهیم آن را در یک جمله خلاصه کنیم، هدف، بهینهسازی و بیشینهسازی ارزش سرمایهگذاری در صنعت نفت است.
سیدسار تصریح کرد: ما باید در قبال هر دلاری که هزینه میکنیم، بیشترین سود و ارزش را خلق کنیم. بهینهسازی، مسیری دائمی و مستمر است و باید بهصورت لحظهای انجام شود. مهندسان اصطلاحی دارند به نام «مدل استاتیک مخزن». یعنی چه؟ شما یک مخزن نفتی را شناسایی میکنید که میلیونها سال پیش در زیر زمین به دام افتاده است. اطلاعاتی از آن بهدست میآورید، آن را مدلسازی میکنید؛ اینکه نفت کجاست؟ چقدر نفت دارد؟ ضخامت لایهها چقدر است؟ چگونه میتوان آن را توسعه داد؟ به این فرایند مدلسازی استاتیک گفته میشود.
وی گفت: اما بهمحض اینکه تولید آغاز میشود، مخزن دیگر استاتیک نیست. فشار تغییر میکند و نفت به سمت نقاط تولید حرکت میکند. اینجا به آن مدل دینامیک میگویند. وقتی با شرایط دینامیک مواجه هستید، باید بهصورت لحظهای پارامترهای مختلف را داشته باشید. باید تاریخچه چاه و مخزن را بدانید، تا بتوانید بهینهسازی انجام دهید.
سیدسار خاطرنشان کرد:در گذشته با رویکرد قدیمی، مطالعات جامع و مفصل میدانی انجام میدادند؛ این فرایند یکساله یا حتی دوساله بود و بر اساس دادههایی صورت میگرفت که از یک سال پیش از شروع مطالعه جمعآوری شده بودند. درحالیکه در همین مدت، شرایط میدان تغییر میکرد. بنابراین نیاز به مرکزی داریم که دادهها را بهصورت لحظهای در اختیار قرار دهد تا بتوان تصمیمات سریع و درست گرفت.
وی ادامه داد: البته تصمیم سریع، الزاماً درست نیست؛ تصمیم درست زمانی اتخاذ میشود که اطلاعات دقیق و صحیح در دسترس باشد. چون اگر اطلاعات اشتباه باشد، تصمیم نیز اشتباه خواهد بود.
سیدسار گفت: نکته مهم دیگر آن است که در صنعت نفت، متخصصان متعددی فعالیت میکنند؛ از زمینشناسان و مهندسان مخزن گرفته تا مهندسان حفاری، تولید، بهرهبرداری و نگهداری. وقتی از یک چاه یا میدان بزرگ حرف میزنیم، همه این افراد باید بهصورت یکپارچه تصمیمگیری کنند. این مرکز برای تحقق همین هدف ایجاد شده است تا همگی بتوانند همزمان و هماهنگ عمل کنند.
وی تصریح کرد: ماژولهای متعددی توسعه دادیم. بهعنوان مثال، برای یکی از چاههای، در عمق 500 تا 600 متری، با فشار و دمای بالا، طراحی و تکمیل آن با چالشهایی همراه بود، بهویژه با توجه به محدودیتهایی که در کشور وجود دارد.
سیدسار تصریح کرد: یکی از اقدامات مهم ما، مانیتورینگ تولید از میدان در حال بهرهبرداری است. همانطور که در ابتدای صحبتها گفتم، هدف ما بیشینهسازی ارزش یک میدان است. ایران دومین دارنده ذخایر گازی و سومین دارنده ذخایر نفتی جهان است. اما صرف دارا بودن ذخایر مهم نیست؛ آنچه اهمیت دارد این است که چگونه این ذخایر را به درآمد و ثروت تبدیل کنیم.
یکی از شاخصهای کلیدی عملکردی ما، پیشبینی تولید برای سه ماه و یک سال آینده است. ما هر روز بررسی میکنیم که آیا پیشبینی ما از تولید با آنچه واقعاً تولید شده تطابق دارد یا نه. اگر تولید طبق پیشبینی صورت گرفته باشد، یعنی سیستم بهدرستی عمل کرده است.
وی گفت: در گذشته، اطلاعات میان واحدهای مختلف در شرکتهای نفتی – بهویژه در بخش دولتی – بهخوبی ردوبدل نمیشد. مهندسان مجبور بودند برای دریافت دادهها نامهنگاری کنند، و اطلاعات در هر واحد بهصورت جداگانه دستهبندی میشد. این موضوع باعث پیچیدگی و ابهام میشد، و گاهی حتی نمیدانستند کدام داده صحیح است.
سیدسار گفت: بهمحض اینکه سیستم رفتاری خارج از انتظار ما از خود نشان دهد، ما در همان لحظه اقدام اصلاحی را انجام میدهیم. این مرکز دقیقاً در راستای همان هدف بهینهسازی و خلق ارزش طراحی شده است.
وی افزود: ما انسانها نمیتوانیم همیشه در محل حضور داشته باشیم، اما این سیستم بهصورت 24 ساعته و آنلاین فعالیت میکند. اطلاعات حتی در بازههای زمانی بهکوتاهی یک ثانیه برای ما ارسال میشود، جمعآوری میشود و سیستم تحلیل میکند. یکی از مزایای این سیستم، تکرارپذیری آن است. یعنی بسیاری از کارهایی که در گذشته بهصورت دستی انجام میشد، حالا به شکل خودکار انجام میشود. ما برای این منظور، سیستم را تعریف و کدنویسی کردیم. با همکاری دانشگاه صنعتی شریف و دیگر دانشگاهها، از متخصصان علوم رایانه بهره گرفتیم و کدنویسیها را انجام دادیم. این سیستم، مهندسی ما را پشتیبانی میکند و کارهایی که پیش از این هر روز تکرار میشد، حالا خودکار انجام میشوند. بنابراین، مهندسان ما زمان خود را صرف فعالیتهای نوآورانهتری میکنند که ارزش بیشتری خلق میکند.
وی تأکید کرد: معمولاً در دستهبندی عمومی، سه سطح برای بلوغ سیستمها در نظر گرفته میشود. سطح ابتدایی آن، سطحی است که در آن ساختار مشخصی وجود ندارد و کارها بهصورت واکنشی انجام میشود؛ یعنی زمانی اقدام میشود که یک مشکل ایجاد شده باشد. اما در سطح بالاتر، سیستم بهگونهای طراحی میشود که بتوان پیش از وقوع مشکل، آن را شناسایی و برای آن اقدام پیشگیرانه تعریف کرد.
سیدسار گفت: شرکتهای نفتی دولتی، چه در ایران و چه در کشورهای دیگر، معمولاً در همان سطوح ابتدایی باقی ماندهاند. آنها نگاه یکپارچهای که من به آن اشاره کردم، نداشتهاند. مثلاً در سازمانها چندین ساختمان وجود دارد که هرکدام مختص یک دپارتمان هستند؛ زمینشناسی، مهندسی مخزن، مهندسی تولید و حفاری، که از هم جدا هستند، اما در توسعه صنعت نفت، همه این واحدها باید در تعامل با یکدیگر باشند.
وی افزود: ما زمانی که وارد فاز توسعه شدیم، حتی پیش از راهاندازی رسمی مرکز، زیرساختهای مانیتورینگ را برای خود تعریف کردیم. ما هدفگذاری کردیم که به سطح بلوغ بالا برسیم، بهصورت یکپارچه کار کنیم، و همه افراد در هر لحظه به اطلاعات دسترسی داشته باشند. در اسفند 1400، موفق شدیم تولید را به 65 هزار بشکه در روز برسانیم.
سیدسار ادامه داد: یک میدانی پیش از انقلاب حفاری شده بود و دیده بودند که شاید تولید اقتصادی نداشته باشد، برای همین علاقهای از سوی شرکت ملی نفت ایران یا سایر شرکتهای خصوصی برای ورود به آن وجود نداشت. اما ما با دو مطالعه جداگانه که در شرکت انجام دادیم، پیشبینی کردیم که امکان تولید تا 50 هزار بشکه در روز وجود دارد. حلقه 4 با تعمیرات وارد مدار شد، چند حلقه دیگر نیز تکمیل شدند و در نهایت به 65 هزار بشکه در روز رسیدیم.
وی تأکید کرد: ما نفتی به میدان نیاوردیم؛ نفت میلیونها سال پیش به زیر زمین رفته و به دام افتاده بود. کاری که ما کردیم، این بود که آن را شناسایی و اکتشاف کردیم، سپس بهصورت یکپارچه مهندسی کردیم و سناریوهای مختلفی که ممکن بود در زیر زمین رخ داده باشد را تحلیل کردیم. حالا دیگر فرآیندها سیستماتیک هستند، یعنی بر اساس یک روال مشخص اجرا میشوند. اگر من نباشم، نفر جایگزین من بتواند کار را ادامه دهد. این یعنی سیستم محور بودن.
وی گفت: پیش از آغاز عملیات، تصمیم گرفتیم ابتدا بررسی کنیم که اصلاً کجای مسیر هستیم. جایگاه شرکتهای ایرانی اکتشاف و تولید را نسبت به شرکتهای بینالمللی بررسی کردیم. در یک سال گذشته، آنالیزهایی انجام دادیم که نشان داد جایگاه ما در برابر شرکتهای جهانی کجاست. شرکتهایی که 20 تا 30 سال پیش این مسیر را آغاز کردهاند.
وی افزود: در حوزه تخصصی فاصله زیادی داریم. سیستم کاری ما معمولاً بسته بوده، اما ارتباطاتی هم داشتهایم. بسیاری از ایرانیانی که در خارج از کشور کار کردهاند، تجربیات ارزشمندی کسب کردهاند و حالا به صنعت نفت ایران برگشتهاند و به ما کمک کردهاند. هرچند این تعداد زیاد نبوده، اما اثرگذار بودهاند.
وی در پایان تصریح کرد: یکی از دلایل اصلی این فاصله، عقبماندگی تکنولوژیک ماست؛ بهویژه در حوزه سختافزار. بسیاری از تکنولوژیهایی که شرکتهای خارجی استفاده میکنند، در دسترس ما نیست. بنابراین متخصصان ما نیز با آن آشنایی ندارند و همین موضوع شکاف ایجاد میکند.
وی گفت: ما یک سال پس از آنالیز اولیه، یعنی حدود شش ماه پیش، به این نتیجه رسیدیم که بخشی از موفقیتهایی که امروز داریم، بهواسطه اقدامات نوآورانه و سرمایهگذاریهایی است که پیشتر انجام دادیم. من با اطمینان میگویم که شرکت پاسارگاد از نظر دانش مهندسی، توسعه و تولید میادین، یکی از بهترین شرکتهای ایرانی است که توان رقابت با شرکتهای خارجی، حتی شرکتهایی مثل آرامکو و برخی شرکتهای آمریکایی که میادین نفتی امارات را توسعه میدهند، دارد.
وی افزود: ما توانستیم تیمی از متخصصان داخلی و بینالمللی را دور هم جمع کنیم و شایستگیمان را در حوزه تکنولوژی ارتقا دهیم. البته باید پذیرفت که اختلافی که ما امروز با دنیا داریم، چه از نظر سرمایهگذاری و چه از نظر سختافزار و تکنولوژی، همچنان وجود دارد. اما نکته مهم این است که این شرکت این اشتیاق را پیدا کرده که روی موضوعات فناورانه و مواد شیمیایی سرمایهگذاری کند.
سیدسار ادامه داد: در حوزه فرهنگ سازمانی هم ما رشد قابل توجهی داشتهایم. اکنون سیستمهایی که در شرکت استفاده میکنیم، قابلیت پایش و تولید مداوم را دارند و این اتفاق بهواسطه یادگیریها و تجربیات سالهای اخیر به دست آمده است.
وی در بخش دیگری از صحبتهایش گفت: یکی از مهمترین گپهایی که ما در آنالیز اولیه تشخیص دادیم، موضوع سرمایهگذاری بود. اگر بخواهیم رشد کنیم، باید سرمایهگذاری کنیم؛ چه در تولید نفت، چه در توسعه تکنولوژی. برای نمونه، شرکت ما تاکنون با هزینه شخصی حدود 10 میلیون دلار سرمایهگذاری کرده که نتایج آن را بهزودی در سطح ملی خواهیم دید.
وی گفت: ما عملاً از نظر حجم اطلاعاتی که در اختیار داریم، قابل مقایسه با شرکت ملی نفت نیستیم. شرکتهایی مانند نفت جنوب که سابقهای 100 ساله دارند، دسترسی کاملی به دادههای میادین دارند. اما ما صرفاً از دادههایی استفاده میکنیم که خودمان از میدان بهدست آوردهایم و همین محدودیت، یکی از گپهای اصلی ما بود.
سیدسار افزود: بر همین اساس پیشبینی کردیم که طی پنج سال آینده نیاز به افزایش تعداد نیروهای متخصص داریم. یا باید نیروهای بیشتری وارد کنیم، یا کار را به سیستمهای تکرارشونده و هوشمند واگذار کنیم؛ سیستمهایی که با سختافزارهایی مانند GPU امکان پایش و کنترل دادههای حجیم را در لحظه دارند.
وی با اشاره به مفهوم تحول دیجیتال گفت: در نهایت، وقتی صحبت از تحول دیجیتال میشود، سطح بلوغ 5 مطرح میشود؛ یعنی جایی که تصمیمگیریها مبتنی بر داده است. در این سطح، پیچیدگی بالاست، اما سیستمها هوشمند میشوند و دادهها خودشان به ما میگویند که چه تصمیمی باید گرفته شود. این یعنی تحول دیجیتال واقعی.
وی افزود: در آنالیزهایی که داشتیم، دیدیم شرکتهای خارجی به ابزارهایی مثل مایکروسافت، گوگل و دیگر شرکتهای بینالمللی دسترسی دارند. اما ما چنین دسترسیهایی نداریم و به همین دلیل به این نتیجه رسیدیم که باید کار را خودمان انجام دهیم.
سیدسار ادامه داد: در همین راستا با دانشگاه شریف و امیرکبیر همکاریهایی را آغاز کردیم و نیروهای متخصص جوان را جذب کردیم. جوانانی که حالا با آموزشهای دادهشده و تلاش خودشان، به دانشمندان داده تبدیل شدهاند.
وی در پایان گفت: مسیر ما از سال 1998 آغاز شد و نزدیک به 20 سال طول کشید تا به سطح دیجیتال برسیم. دلیل این زمانبر بودن، محدودیتهایی در تکنولوژی و قیمت سنسورها در گذشته بود. اما امروز فناوریها با سرعت بالایی رشد کردهاند، قیمتها کاهش یافته و شرکتها به سمت استفاده از دادههای لحظهای حرکت کردهاند تا بهرهوری را بالا ببرند و هزینههای عملیاتی را کاهش دهند.
سیدسار گفت: ما در این مسیر به دنبال ارزشآفرینی از طریق کاهش هزینه تولید بودیم. یکی از اقدامات ما افزایش عمر مفید تجهیزات و بهرهبرداری بهینه از منابع بود؛ مثل خودرویی که اگر نگهداری مناسبی داشته باشد، عمر و بازدهی بالاتری خواهد داشت.
وی افزود: ما با بهرهگیری از طراحی مهندسی مناسب، استفاده از تکنولوژی روز و مانیتورینگ هوشمند سیستم، توانستیم نگهداری را در سطحی متفاوت از گذشته انجام دهیم. البته در کشور ما هم میادینی نظیر سروش و سیری وجود دارد که اطلاعات محدودی از آنها قابل دسترسی است، اما ما از این مرحله عبور کردهایم.
به گفته وی، شرکت در مسیر دیجیتالسازی، صرفاً به جمعآوری دادهها بسنده نکرده، بلکه با تحلیل و تشخیص دقیق، فرآیندها را بهصورت هوشمند مدیریت کرده است. او ادامه داد: در دیماه 1400، تصمیم گرفتیم فاز دیجیتالسازی را اجرایی کنیم و به فضل الهی آن را به بهرهبرداری رساندیم.
سیدسار در ادامه درباره اندازهگیری تولید توضیح داد: برای محاسبه دقیق میزان تولید، نیاز به نصب سنسورهایی در محل وجود دارد که هم هزینهبر هستند و هم درصدی از عدم قطعیت را به همراه دارند. به همین دلیل، ما اطلاعات مربوط به فشار و دمای مخزن را مبنا قرار دادهایم تا تخمین دقیقی از میزان تولید داشته باشیم.
وی با ذکر مثالی گفت: در یکی از چاههای ما، نفت از عمق 4600 متری با دمای اولیه حدود 137 درجه سانتیگراد بالا میآید و روزانه نزدیک به شش هزار بشکه تولید میشود. تا زمانی که به سطح میرسد، دما به حدود 106 درجه کاهش مییابد. در همین چاه، فشار عملیاتی حدود 65 بار است که عدد بسیار بالایی محسوب میشود و کنترل آن نیازمند مهارت و دقت بالا است.
به گفته وی، یکی دیگر از اقدامات انجامشده در این پروژه، کاهش کلاس کاری خطوط لوله با هدف مدیریت ایمن فشار و افزایش تابآوری زیرساختها بوده است. او افزود: برای انتقال نفت از محل چاه تا کارخانه، بسته به موقعیت، بین دو تا ده کیلومتر خط لوله احداث شده است. طراحی این خطوط بهگونهای است که در صورت افزایش ناگهانی فشار، سیستم بهصورت خودکار وارد عمل شده و از آسیب به تجهیزات پاییندستی جلوگیری میکند.
وی خاطرنشان کرد: در این سیستم، ایمنی بهطور کامل رعایت شده است. حتی اگر خداینکرده حادثهای رخ دهد، سازوکارهایی طراحی شدهاند تا در کوتاهترین زمان، وضعیت تحت کنترل قرار گیرد و از آسیبهای احتمالی جلوگیری شود.
سیدسار گفت: سیستم ما حتی دما و رطوبت را نیز پایش میکند و در صورت بروز هرگونه خطای اپراتوری مانند باز و بسته شدن اشتباه شیر، هشدار میدهد.» او با اشاره به قابلیت تعریف آلارم برای هر یک از پارامترها افزود: «این سیستم فقط برای کنترل تولید نیست، بلکه با تحلیل لحظهای دادهها، امکان تصمیمگیری سریع را فراهم میکند.
وی با اشاره به محدود بودن تعداد این سیستمها در کشور اظهار کرد: از زمانی که ما در حدود چهار سال پیش با یک شرکت چینی همکاری کردیم، هزینهها تقریباً دو برابر شده و از 10 میلیون دلار به حدود 20 میلیون دلار رسیده است. این افزایش قیمت عمدتاً به دلیل هزینههای بالای خدمات و سرویسهای مورد نیاز بوده است.
سیدسار افزود: ما از این تکنولوژی در مانیتورینگ حفاری چاههای نفت و گاز استفاده میکنیم. با نصب سنسورها، اطلاعات فشار، دما و رفتار سیالات در اختیار ما قرار میگیرد. در حال حاضر، سیستم ما دادههایی با دقت بالا ثبت میکند که به ما در بهینهسازی حفاری و مدیریت مخزن کمک میکند.
وی با اشاره به همکاری نزدیک با شرکت ملی حفاری گفت: اگر تمام شرکتهای خصوصی را نیز در نظر بگیریم، مجموع حفاریهای کشور سالانه به حدود 150 حلقه چاه میرسد. در بهترین حالت، این تعداد میتواند حدود 200 هزار بشکه به ظرفیت تولید کشور اضافه کند، در حالیکه افت طبیعی تولید نیز باید جبران شود.
سیدسار ادامه داد: برای رسیدن به تولید 6 میلیون بشکه در روز، کافی نیست که فقط چاه جدید حفر کنیم. باید با سیستمهای دیجیتال و تحلیل داده، بهرهوری را بالا ببریم. یکی از اقدامات ما، خرید تجهیزات جدید برای خشکی و اضافه کردن یک دکل دریایی بوده است.
وی تصریح کرد: در گذشته شناخت ما از برخی مناطق زیرزمینی بسیار کم بود، اما با نصب این سیستمها و دریافت دادههای دقیق، توانستیم شناخت عمیقتری بهدست آوریم و عملیاتها را به موقع و مؤثر انجام دهیم.
سیدسار درباره اثرگذاری نصب این سیستم گفت: زمانی که نرخ تولید از یک چاه به 6 هزار بشکه در روز رسید، این در حالی بود که بدون اقدامات اصلاحی، ممکن بود چاه فقط 15 روز تولید داشته باشد. با استفاده از دادههای این سیستم، توانستیم به موقع تصمیمگیری کنیم و تولید را در اسفند ماه به بیش از 8 هزار بشکه در روز برسانیم.
وی خاطرنشان کرد: در یک نمونه مشخص، اگر سیستم نصب نمیشد، شاید تنها 3500 بشکه تولید داشتیم، اما با اجرای بهموقع عملیات اصلاحی، ارزش افزودهای معادل یک میلیون دلار ایجاد شد. این سیستمها کمک میکنند تا در کوتاهترین زمان ممکن تصمیمات بهینه بگیریم و از افت تولید جلوگیری کنیم.
وی درباره عملکرد سامانه و نتایج حاصل از آن گفت: نمودار سبز در مقایسه با نمودار قرمز نشان میدهد که ما در بازه زمانی مشخص، چه میزان بشکه نفت بیشتری تولید کردهایم. اگر اقدامات بهموقع را انجام نمیدادیم، تولید روی خط قرمز حرکت میکرد.
وی ادامه داد: در برخی مقاطع، خط قرمز بالا میرود، چون در آن مقاطع هزینههایی انجام دادیم تا تولید بیشتری داشته باشیم. اما در مجموع با کمک این مرکز، توانستیم تولید میدان را افزایش دهیم.
به گفته وی، در کشور ما، هر سیستم بین 5 تا 25 درصد ظرفیت بهینهسازی دارد و گاهی حتی این عدد از 25 درصد نیز بیشتر میشود. هیچ سیستمی وجود ندارد که بگوییم امکان بهبود ندارد.
سیدسار با اشاره به اقدامات انجامشده در برخی میادین خاطرنشان کرد: در چند میدان اقدامات مؤثری انجام دادهایم که منجر به افزایش تولید شده است. برای مثال، در یکی از میادین با استفاده از تجربههای قبلی توانستیم حدود 1400 بشکه در روز به تولید اضافه کنیم. این افزایش بهتنهایی ارزشی حدود 15 میلیون دلار ایجاد کرده است.
وی تأکید کرد: در مواردی، تولید از 1500 بشکه در روز به بیش از 3200 بشکه افزایش یافته است. این پروژه در سال 2024 انجام شد و هنوز هم ادامه دارد.
سیدسار درباره ساختار ارتباطات و انتقال دادهها توضیح داد: شبکه داخلی ما بهگونهای طراحی شده که حتی اگر ارتباط اینترنتی قطع شود، دادهها ذخیره میشوند و در دسترس هستند. ما به تمام دادهها دسترسی داریم و توانستهایم اطلاعات کامل را از این طریق جمعآوری کنیم.
وی در پاسخ به پرسشی درباره نوع قراردادها و نحوه تعامل با شرکت ملی نفت گفت: ما قرارداد 20 ساله برای توسعه و تولید از میادین داریم. شرکت ما در حال حاضر از دو میدان استفاده میکند و قراردادهای بلندمدت دارد. ورود شرکتهای دیگر هم ممکن است، اما نیاز به توانمندی و سرمایهگذاری دارد.
وی ادامه داد: ما در سالهای 1394 تا 1396 سومین قرارداد نفتی را بستیم و نخستین شرکت ایرانی بودیم که قراردادی 100 درصدی با دو میدان امضا کرد. در این قرارداد بالغ بر 350 میلیون دلار سرمایهگذاری انجام شد. در بند قرارداد آمده بود که اگر به تولید 21 هزار و 800 بشکه در روز نرسیم، باید پاسخگو باشیم.
به گفته وی، در حال حاضر این قرارداد در حال اجراست و همزمان با توسعه میدان، بستر سرمایهگذاری برای سایر شرکتها نیز فراهم شده است. ما همچنین خدمات فنی را به دیگر شرکتها ارائه میدهیم.
سیدسار درباره استفاده از فناوریهای نوین توضیح داد: در طراحی مرکز داده، از مدلهای زبانی بزرگ برای تحلیل و مدیریت اطلاعات استفاده کردهایم. بخشی از این سامانهها در اختیار مدیران شرکت ملی نفت و شرکتهای خصوصی قرار میگیرد تا آنها نیز بتوانند از اطلاعات استفاده کنند.
وی افزود: در حال آمادهسازی بستری هستیم که همزمان 100 نفر بتوانند به دادهها دسترسی داشته باشند. اطلاعات فنی، مهندسی و تخصصی در این مرکز تجمیع شده و امکان تحلیل لحظهای آنها فراهم است.
سیدسار در پایان خاطرنشان کرد: با وجود اینکه زبان اصلی این سیستمها انگلیسی است، تلاش کردهایم محتوای تخصصی مرتبط با کشور ایران را نیز وارد کنیم تا متخصصان داخلی و خارجی بتوانند به طور همزمان از آن استفاده کنند؛ مشابه سامانههایی که در حوزه آب و برق وجود دارد.
انتهای پیام/
منبع: tasnim